Machine downtime is a big problem for companies dealing with automated operations and heavy machinery. Breakdowns can hinder production, result in loss of funds, and even cause safety risks. Industries are therefore seeking protective systems that ensure maximum machine uptime and give trouble-free operations. Protective systems use advanced technologies meant to safeguard equipment against damage and offer continuous operation. The systems run in real-time to keep your machines up and running.
Condition Monitoring
Condition monitoring is a critical aspect of Enhancing Machine Uptime with Protective Systems in the contemporary industrial era, consisting of continuous measurement of the performance and condition of machines. Vital parameters such as vibration, temperature, pressure, and fluid level are continuously measured by industries utilizing advanced sensors and diagnostic computer software. The data-based process provides an early indication of mechanical failure, thereby allowing preventative maintenance prior to failure.
Condition Monitoring Techniques:
- Vibration Analysis: Suggests misalignment, imbalance, and bearing fault, which, unless corrected, can lead to costly damage to machinery.
- Thermal Imaging: Thermal cameras scan parts to detect rising temperature levels and indicate possible electrical or mechanical failure.
- Oil Analysis: Analyzes lubricants for wear metals, impurities, and loss of viscosity, signaling internal part wear.
- Ultrasonic Testing: Identifies leakage, cracks, and material imperfections not observable otherwise, providing structural integrity.
The implementation of condition monitoring methods enables producers to change from reactive maintenance to proactive maintenance, which shortens unexpected downtime, reduces repair costs and extends equipment lifetime. Predictive analytics allows companies to shorten maintenance optimization schedules, thus leading to operational improvements in both efficiency and productivity.
Predictive Maintenance
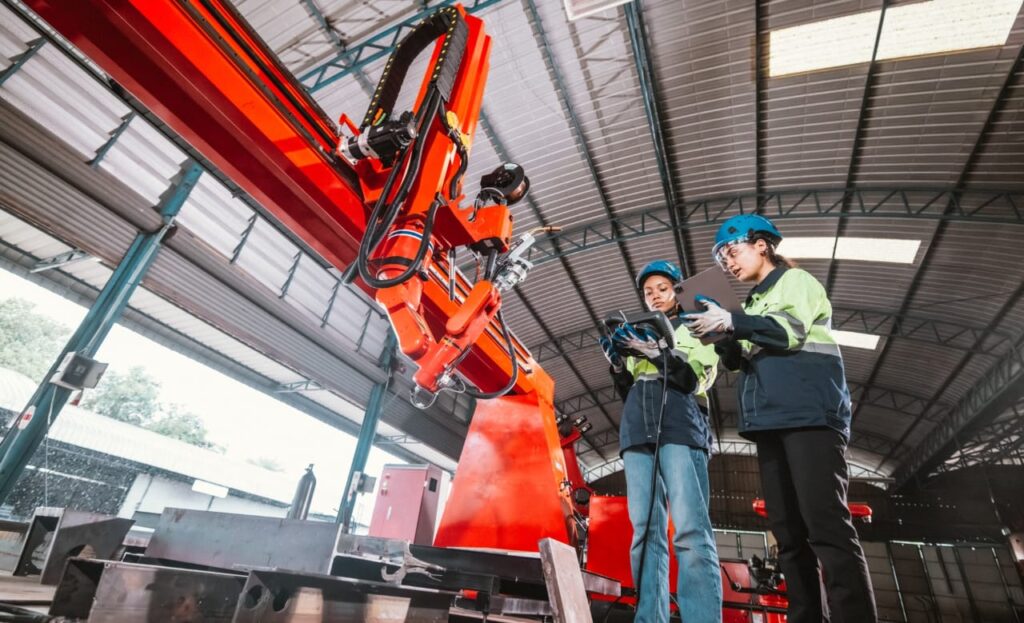
The advanced preventive method of predictive maintenance (PdM) predicts equipment breakdowns by collecting data through machine learning technology combined with real-time sensors. The real-time functioning of equipment directs PdM to create maintenance specifications while it replaces the schedule-based approach of preventive maintenance by optimizing repair operations.
How Predictive Maintenance Helps:
- Early issue detection through PdM helps manufacturers avoid unplanned equipment breakdowns, which sustains continuous operations.
- Participating in PdM practices results in decreased maintenance expenses because organizations can resolve problems before they reach crisis levels.
- Early equipment maintenance interventions extend equipment lifespan by avoiding excessive wear and damage to the machines.
- Operational efficiency increases because better asset utilization leads to both elevated productivity levels and diminished energy expenses.
PdM functions because of the combination of three major advanced technologies. These include the Internet of Things (IoT), artificial intelligence (AI), and cloud computing. The system records real-time data points about temperature together with vibration and pressure through sensor networks that enable AI applications to detect unusual behaviors before predicting equipment failures. The implementation of PdM allows industries to transform from dependent maintenance to data-based management methods, thus promoting safety, reliability and cost reductions.
Thermal Protection
Machines require thermal protection systems to stop excessive heating that causes both mechanical breakdowns and decreased operational efficiency as well as electrical breakdowns. Industrial processes place temperature control at the center of operation because high temperatures degrade equipment parts while cutting down tool longevity and creating more fire risk.
Thermal Protection Methods:
- Heat Sensors: They continuously monitor temperature levels and raise alarms or alerts when safe working limits are exceeded, allowing timely action.
- Cooling Systems: Various cooling systems, such as fans, heat exchangers, and liquid cooling systems, help dissipate excess heat and maintain optimal temperatures.
- Automatic Shutdowns: In the event of severe overheating, automatic shutdown systems turn off equipment to prevent costly damage and repair.
Industrial success depends on thermal protection systems which combine long-lasting equipment performance with better operational safety and efficiency. The active management of heat allows organizations to reduce unexpected downtime and save energy since it stops unnecessary power usage from heat-related failures.
Overload Protection
Machines requiring overload protection devices need these components to ensure they avoid dangerous stress levels that produce premature breakdowns together with high maintenance costs and poor operational efficiency. The operation of machines beyond their limits causes them to experience elevated temperatures as well as structural failure and breakdowns. Machines remain free from harm because industries utilize specialized protection methods against overload conditions to preserve safety.
Overload Protection Techniques:
- Circuit Breakers and Fuses: They detect overloads of electric current and cut off the power supply to prevent overheating, short circuits, and electrical fires.
- Torque Limiters: In mechanical use, torque limiters interrupt power transmission if the torque levels reach above safety levels, preventing gears, shafts, and motors from damage.
- Load Sensors: The sensors monitor weight, pressure, and force being applied to equipment and machines to prevent mechanical overload and maintain the equipment operating at safety loads.
Company protection systems enable organizations to remove equipment stoppages and reduce maintenance costs while extending equipment operational periods. High-output installations are accompanied by risk at factory facilities, construction sites, and power generation plants, which makes overload protection especially crucial. The operation runs best and causes minimal disruptions through the utilization of the perfect overload protection system.
Emergency Shutdown Mechanisms
Emergency shutdown systems (ESD) function as critical security devices which activate automatic equipment shutdown when dangerous circumstances occur. These systems protect operations completely against manufacturing issues as well as workplace accidents and severe industrial incidents. The shutdown function activates automatically to prevent incidents from worsening, which safeguards human beings and property.
Components of Emergency Shutdown Systems:
- Emergency Stops by Hand: Push-button stops allow the operator to trigger an immediate machine stop in emergencies, providing instantaneous action as required.
- Automatic Safety Interlocks: With control logic and sensors, safety interlocks track essential failures high pressure, temperature overload, or mechanical failure and automatically trigger a shutdown.
- Redundant Power Supplies: During a power outage, redundant power supplies guarantee that shutdown processes can be executed safely, avoiding uncontrolled machine operation.
Installation of emergency shutdown systems takes place mostly in oil and gas operations along with manufacturing and power generation facilities because minor procedural errors can result in widespread catastrophe. A well-implemented ESD system delivers both better workplace security and improved industrial standards, which minimizes the potential for court actions and financial losses.
Industrial operations depend on continuous machine operation to maintain market leadership. Protective systems reach their goal by preventing failures, maintaining equipment, and scheduling maintenance in a timely manner. Organizations that invest in condition monitoring, together with predictive maintenance overload protection, emergency shutdown systems, and remote monitoring capabilities, experience decreased downtime cost savings and higher operational efficiency.